Cite report
IEA (2020), CCUS in Clean Energy Transitions, IEA, Paris https://www.iea.org/reports/ccus-in-clean-energy-transitions, Licence: CC BY 4.0
Report options
CCUS technology innovation
Highlights
- The extent to which CCUS will be able to contribute to achieving net-zero emissions hinges in large part on technological progress. The maturity of CCUS varies considerably by technology type and application: several technologies are already mature and could be scaled up rapidly in applications such as coal-fired power generation and hydrogen production, while others require further development.
- Two-thirds of the cumulative emissions reductions from CCUS through to 2070 in the Sustainable Development Scenario relative to the Stated Policies Scenario come from technologies that are currently at the prototype or demonstration stage. Given the time lags involved, innovation needs to be stepped-up now to ensure key applications are commercially available in the coming decade.
- There is a disconnect between the level of maturity of individual CO2 capture technologies and the areas in which they are most needed. For example, the most advanced technology for CO2 capture in the cement industry is only at the demonstration stage, but a lack of alternative technology options means CCUS is needed to deliver 60% of the sector’s emissions reductions in the Sustainable Development Scenario. Other CCUS applications that will require a major innovation push include chemicals and steel production, gas-fired power generation, BECCS and DAC.
- Transport and storage of CO2 has been demonstrated for several decades but innovation can improve existing technologies and unlock new opportunities, including large-scale shipping of CO2 and more advanced technologies for long-term monitoring of stored CO2. Innovation in CO2 use applications, including for synthetic fuels and chemicals, will be important to secure cost reductions.
- The theoretical capacity for storing CO2 in deep geological formations globally is vast and far exceeds that required to reach net-zero emissions; in the Sustainable Development Scenario, only 3% of potential global storage capacity is used. Further exploration and assessment will be critical to provide confidence in the availability of CO2 storage in key regions.
Technology readiness along the CCUS value chain
The capture, transport and utilisation or storage of CO2 as a successful mitigation strategy hinges on the availability of technologies at each stage of the process as well as on the development and expansion of CO2 transport and storage networks. All of the steps along the value chain need to be technologically ready and developed in tandem for CCUS to scale up.
CCUS technologies are at varying levels of maturity today. Several technologies in CO2 capture, transport, utilisation and storage are already deployed at large scale, but other technologies, including those that hold out the promise of better performance and lower unit costs, require further development. One way to assess where a technology is in its journey from the laboratory to the marketplace is to use the TRL scale, which provides a common framework that can be applied to any technology to assess and compare the maturity of technologies across and within different sectors.
Technology readiness level scale
Originally developed by the United States National Aeronautics and Space Administration (NASA) in the 1970s, the TRL provides a snapshot in time of the level of maturity of a given technology within a defined scale. It is now widely used by research institutions and technology developers around the world to set research priorities and design innovation support programmes. The scale, which ranges from 1 to 9, can be applied to any technology. However, arriving at a stage where a technology can be considered commercially available (TRL 9) is not sufficient to describe its readiness to meet energy policy objectives, for which scale is often crucial. For this reason, the IEA has extended the TRL scale used in this report to incorporate two additional levels of readiness: one where the technology is commercial and competitive but needs further innovation efforts for the technology to be integrated into energy systems and value chains when deployed at scale (TRL 10), and a final one where the technology has achieved predictable growth (TRL 11). The TRLs are grouped in this report into four broader readiness categories: prototype, demonstration, early adoption and mature. All of the CCUS technologies and CCUS value chains that are projected to play a role in the Sustainable Development Scenario before 2070 are already at least at the prototype stage. For more details, see IEA (2020a) and IEA (2020b).
Mature for commercial technology types that have reached sizeable deployment and for which only incremental innovations are expected. Technology types in this category have all designs and underlying components at TRL 11. Hydropower and electric trains are examples.
Early adoption for technology types for which some designs have reached market and require policy support for scale-up, but where there are competing designs being validated at the demonstration and prototype stages. Technology types in this category have an underlying design of TRL ≥ 9. Offshore wind, electric batteries and heat pumps are examples.
Demonstration for technology types for which designs are at demonstration stage or below, meaning no underlying design at TRL ≥ 9, but with at least one design at TRL 7 or 8. Carbon capture in cement kilns, electrolytic hydrogen-based ammonia and methanol, and large long-distance battery-electric ships are examples.
Prototype for technology types for which designs are at prototype stage of a certain scale, meaning no underlying design at TRL 7 or 8, but with at least one design at TRL 5. Ammonia-powered vessels, electrolytic hydrogen-based steel production and DAC are examples.
Technology readiness level scale applied by the IEA
Open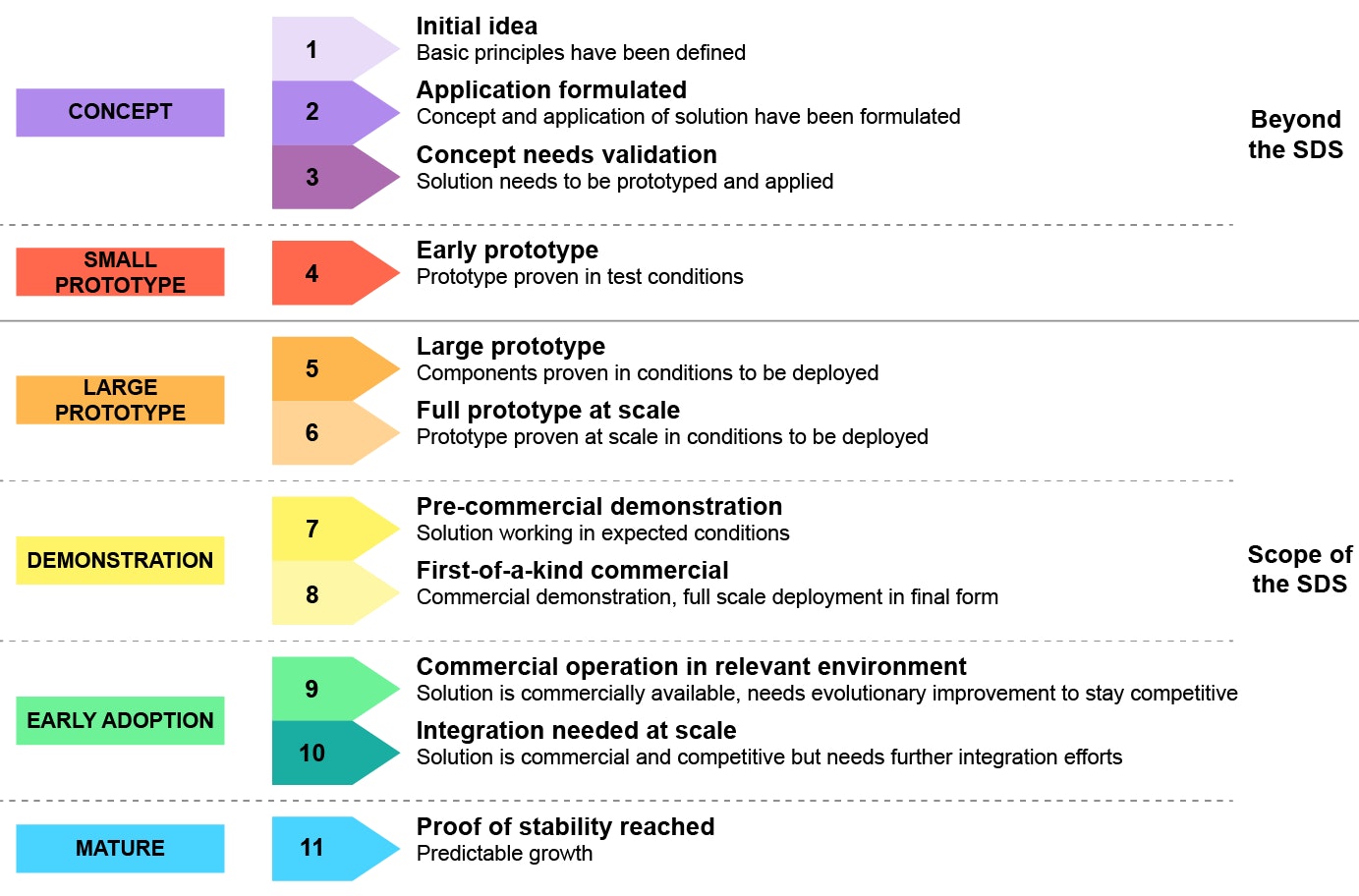
The TRLs and categories used in this report (prototype, demonstration, early adoption and mature) refer not only to the stages of technological development, but also to their adoption in the market. Most technologies that are at the early adoption stage today have already gone through the full technological development cycle, but have not been labelled as “mature" because they have not been widely deployed yet – as is the case for most CCUS applications. A broad range of technologies therefore fall into the “early adoption” category, including many advanced CCUS technologies but also renewable technologies such as electric vehicles, onshore wind and solar PV, which are commercial and competitive but require further integration efforts. Technologies in the early adoption category can be scaled up rapidly once the necessary policy and legal framework conditions are in place.
TRL of select technologies along the CCUS value chain
Open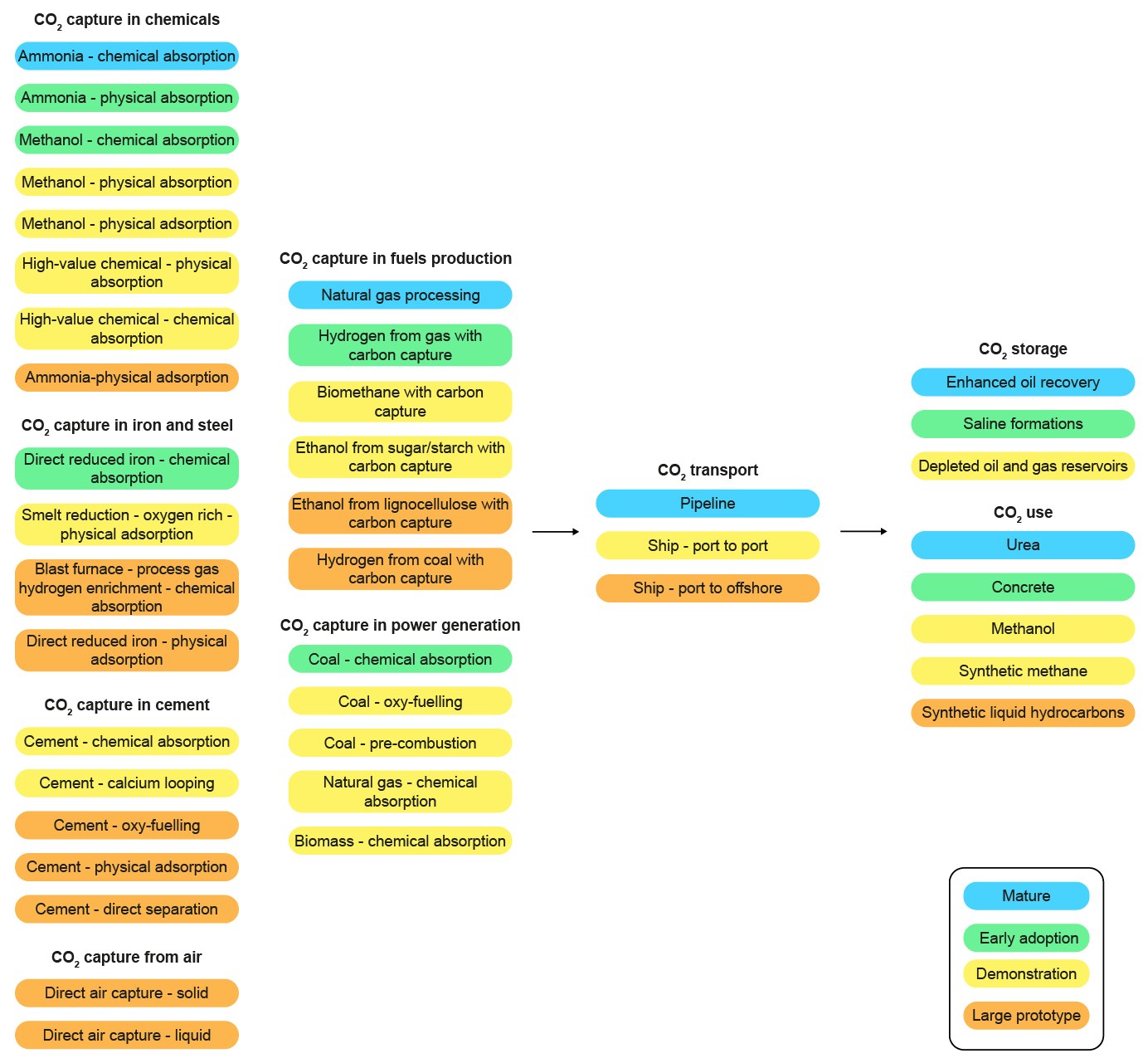
Several applications of CCUS are already widely deployed today, including chemical absorption of CO2 from ammonia production and natural gas processing, CO2 use in the production of fertiliser (urea), and long-distance pipeline transport and injection of CO2 for EOR. A number of other applications have been demonstrated at scale over the last decades, but are still at the early adoption stage, such as chemical absorption from coal-fired power generation and hydrogen production from natural gas, compression of CO2 from bioethanol production and coal-to-chemicals plants, and CO2 storage in saline aquifers. Several other applications, including DAC and CO2 capture from cement and iron and steel making, are still at the demonstration or prototype stage. In each of these potential new applications, a range of CO2 capture technologies need to be tailored to the particular conditions of each individual process.
In the Sustainable Development Scenario, nearly two-thirds of the cumulative emissions reductions from CCUS through to 2070 relative to the Stated Policies Scenario come from technologies that are currently at the prototype or demonstration stage. The other one-third comes from technologies that are already mature or at the early adoption stage, which can be scaled up rapidly, bringing forth incremental technological improvements and cost savings. In the decade to 2030, such technologies in power and fuel transformation, including hydrogen production, contribute around half of the cumulative emissions savings in the Sustainable Development Scenario. Most of these applications are based on chemical absorption as the CO2 capture technology, with this already widely used in commercial capture facilities and embedded in demonstration plants today.
World CO2 emissions reductions from CCUS by technology readiness category in the Sustainable Development Scenario relative to the Stated Policies Scenario, 2018-2070
OpenMajor improvements to a wide range of technologies that are at the prototype or demonstration stage today are needed. Important applications that start to play a pivotal role in the next decade or so, but that still require a near-term push from RD&D, include chemical absorption from gas-fired power generation and cement and chemicals production, BECCS and CO2 capture from iron and steel manufacturing. Some applications have multiple technology maturities as they represent several sub‑applications with different capture technologies (e.g. coal power generation), or different energy conversion or production processes from which the CO2 is captured (e.g. other fuel transformation, chemicals, and iron and steel).
World cumulative CO2 emission reductions from CCUS by application and technology readiness in the Sustainable Development Scenario relative to the Stated Policies Scenario, 2020-2070
OpenDAC and CO2 conversion to synthetic hydrocarbon fuels, which play important roles later in the projection period, also require considerable further RD&D to ensure that they can start to be deployed at scale from the 2030s. Efforts to develop DAC early can provide an important technology hedge against the risk of slower-than-expected innovation or commercialisation of other technologies.
CO2 capture
CO2 capture is an integral part of several industrial processes and, accordingly, technologies to separate or capture CO2 from flue gas streams have been commercially available for many decades. The most advanced and widely adopted capture technologies are chemical absorption and physical separation; other technologies include membranes and looping cycles such as chemical looping or calcium looping. In practice, the most appropriate capture technology for a given application depends on a number of factors, including the initial and final desired CO2 concentration, operating pressure and temperature, composition and flow rate of the gas stream, integration with the original facility, and cost considerations.
Principal CO2 capture technologies
Chemical absorption of CO2 is a common process operation based on the reaction between CO2 and a chemical solvent (such as compounds of ethanolamine). This operation is usually performed using two columns, one for the absorption and the other operating at a higher temperature, releasing pure CO2 and regenerating the chemical solvent for further operation. Chemical absorption using amine-based solvents is the most advanced CO2 separation technique (TRL 9-11). It has been widely used for decades and is currently applied in a number of small and large-scale projects worldwide in power generation (e.g. Boundary Dam in Canada and Petra Nova in the United States), fuel transformation (e.g. Quest in Canada) and industrial production (e.g. Al Reyadah CCUS project and Japan’s COURSE50 Project in steel production, the Enid Fertilizer Plant in the United States and the Uthmaniyah CO2-EOR demonstration project in Saudi Arabia). There are also other large-scale CCUS projects currently planned (e.g. cement production in Norway, waste-to-energy in Norway and The Netherlands) which will all be using chemical absorption for CO2 separation.
Physical separation of CO2 is based on either adsorption, absorption, cryogenic separation, or dehydration and compression. Physical adsorption makes use of a solid surface (e.g. activated carbon, alumina, metallic oxides or zeolites), while physical absorption makes use of a liquid solvent (e.g. Selexol or Rectisol). After capture by means of an adsorbent, CO2 is released by increasing temperature (temperature swing adsorption [TSA]) or pressure (pressure swing adsorption [PSA] or vacuum swing adsorption [VSA]).
Physical separation is currently used mainly in natural gas processing and ethanol, methanol and hydrogen production, with nine large plants in operation (TRL 9-11), all of them in the United States. They typically employ proprietary solvents (at the Century Plant in Texas, the Great Plains Synfuels Plant in North Dakota, the Lost Cabin Gas Plant in Wyoming, and the Terrell Natural Gas Processing Plant in Texas), VSA (Air Products’ carbon capture from hydrogen production facility in Texas) or cryogenic separation techniques (the Shute Creek Gas processing plant in Wyoming). The Illinois Industrial Carbon Capture and Storage Project is the largest CCUS facility applied to biofuels production and relies on dehydration and compression (due to the composition of the gas stream, exclusively CO2 and water), while the Coffeyville Gasification Plant uses CO2 physical separation through separation and compression of highly concentrated CO2 streams.
Oxy-fuel separation involves the combustion of a fuel using nearly pure oxygen and the subsequent capture of the CO2 emitted. Because the flue gas is composed almost exclusively of CO2 and water vapour, the latter can be removed easily by means of dehydration to obtain a high-purity CO2 stream. Typically, oxygen is produced commercially via low-temperature air separation, which is energy-intensive. Lowering the energy consumption of this step and of the overall oxy-fuel process are, therefore, key factors in reducing capture costs. Advanced concepts with potential for cost reduction include oxy-fuel gas turbines (used within supercritical CO2 power cycles) and pressurised oxy-fuel CO2 capture, both of which make more efficient use of materials and are thus potentially cheaper to build and operate. The technology is currently at the large prototype or pre‑demonstration stage (TRL 5 to 7). A number of projects have been completed in coal-based power generation (the Callide project in Australia and the Compostilla project in Spain) and in cement production (HeidelbergCement’s Colleferro plant in Italy, LafargeHolcim’s Retznei plant in Austria and the Cement Innovation for Climate facility in Germany).
Membrane separation is based on polymeric or inorganic devices (membranes) with high CO2 selectivity, which let CO2 pass through but act as barriers to retain the other gases in the gas stream.1 Their TRLs vary according to the fuel and application. In natural gas processing, they are mainly at the demonstration stage (TRL 6-7). The only existing large-scale capture plant based on membrane separation is operated by Petrobras in Brazil. Membranes for CO2 removal from syngas and biogas are already commercially available, while membranes for flue gas treatment are currently under development (He, X. et al., 2017). Several membrane technologies for CO2 separation have been tested in the United States through collaborations between the National Carbon Capture Center and various partners including the Gas Technology Institute, the Department of Energy’s National Energy Technology Laboratory, Membrane Technology and Research, and France’s Air Liquide.
Calcium looping is a technology that involves CO2 capture at a high temperature using two main reactors. In the first reactor, lime (CaO) is used as a sorbent to capture CO2 from a gas stream to form calcium carbonate (CaCO3). The CaCO3 is subsequently transported to the second reactor where it is regenerated, resulting in lime and a pure stream of CO2. The lime is then looped back to the first reactor. Calcium looping technologies, currently at TRL 5-6, have been tested, mostly at the pilot plant scale, for coal-fired fluidised bed combustors and cement manufacture. Two European projects are developing calcium looping capture technologies in steel (C4U) and cement production (CLEANKER) at pilot and pre‑commercial scales.
Chemical looping is a similar two-reactor technology. In the first reactor, small particles of metal (e.g. iron or manganese) are used to bind oxygen from the air to form a metal oxide, which is then transported to the second reactor where it reacts with fuel, producing energy and a concentrated stream of CO2, regenerating the reduced form of the metal. The metal is then looped back to the first reactor. Chemical looping technologies have been developed by academia, research organisations and several companies, including manufacturers operating in the power sector. This has led to the development and operation of around 35 pilot projects (TRL 4-6) with capacity up to 3 MW for coal, gas, oil and biomass combustion (IEAGHG, 2019a).
Direct separation involves the capture of CO2 process emissions from cement production by indirectly heating the limestone using a special calciner (TRL 6). This technology strips CO2 directly from the limestone, without mixing it with other combustion gases, thus considerably reducing energy costs related to gas separation. The Low Emissions Intensity Lime and Cement (LEILAC) pilot plant developed by Calix at the HeidelbergCement plant in Lixhe, Belgium, is one example where this technology is being applied in practice (LEILAC, 2019).
While in conventional thermal power plants, flue gas or steam is used to drive one or multiple turbines, in supercritical CO2 power cycles, supercritical CO2 (i.e. CO2 above its critical temperature and pressure) is used instead. Supercritical CO2 turbines typically use nearly pure oxygen to combust the fuel, in order to obtain a flue gas composed of CO2 and water vapour only. Two supercritical CO2 power cycles are currently in operation: NET Power’s Allam cycle and the Trigen Clean Energy Systems (CES) cycle (TRL 5-7). The 50 MW NET Power plant in Texas started operations in 2018, while a 300 MW commercial plant is currently at the design phase. The 150 MW CES plant at the Kimberlina power station in California has been operating successfully since 2013.
The cost of capturing CO2 can vary significantly, mainly according to the concentration of CO2 in the gas stream from which it is being captured, the plant’s location, energy and steam supply, and integration with the original facility (Ferrari et al., 2019; IEAGHG, 2018c). For some processes, such as ethanol production or natural gas processing or after oxy-fuel combustion in applications such as power generation or cement, CO2 can be already highly concentrated. This CO2 can be simply pre-treated if necessary (e.g. dehydration) and then compressed for transport and storage or use at relatively low cost. For example, the cost of separating out the CO2 contained in natural gas – which is often required for technical reasons before the gas can be sold or liquefied – can be as low as USD 15/t to USD 25/t2 For more diluted CO2 streams, including the flue gas from power plants (where the CO2 concentration is typically the 3-14%) or a blast furnace in a steel plant (20-27%), the cost of CO2 capture is much higher (over USD 40/t of CO2 and sometimes more than USD 100/t, accounting on average for around 75% of the total cost of CCUS (NPC, 2019).3
Levelised cost of CO2 capture by sector and initial CO2 concentration, 2019
OpenMost CO2 capture systems have been designed to capture around 85-90% of the CO2 from the point source, which results in the lowest cost per tonne of CO2 captured. However, in a net-zero energy system, higher capture rates – approaching 100% – will be needed. This is technically and economically achievable according to recent studies.
The role of high CO2 capture rates
To date, the developers of technology to capture CO2 from low-concentration gas streams, such as flue gas from power stations or industrial furnaces (where the CO2 makes up 3% to 14% by volume) have generally aimed for capture rates of 85% to 90%. These rates result in the lowest cost per tonne of CO2 captured (Rao and Rubin, 2006). For example, the two large-scale CCUS projects in the power sector – the coal-based Boundary Dam and Petra Nova projects in North America – are designed to separate out around 90% of the CO2 from the flue gas. Similar capture rates are applied in nearly all demonstration and pilot plants (IEAGHG, 2019b). In a net-zero emissions energy system, the residual emissions from fossil fuel-based power plants and industrial facilities would have to be mitigated as well, either by raising CO2 capture rates, by co‑firing biomass, or by integrating other carbon removal options.
There are no technical barriers to increase capture rates well beyond 90% for most mature capture technologies. In fact, natural gas processing today requires very high capture rates to meet product gas specifications for pipeline transport (typically less than 0.5% CO2 by volume) and liquefaction (0.005% CO2 by volume). While capturing 100% of the CO2 is often prohibited by thermodynamic laws, capture rates of 98% or higher are technically feasible, but require modifications of the CO2 separation process. These modifications typically include larger equipment, multiple process steps and higher energy consumption per tonne of CO2 captured, which increases unit costs. The technical implications and costs of higher capture rates are best understood for chemical absorption systems. CO2 capture rates as high as 99% can be achieved at comparably low additional marginal cost. For instance, increasing CO2 capture rates for chemical absorption from 90% to over 99% increases capture costs by only 4% for coal-based and around 10% for gas-based power generation (IEAGHG, 2019b).
Indicative CO2 capture costs for coal and gas-fired power plants by capture rate
OpenHigh capture rates become the dominant CCUS technology in the power sector and heavy industry in the Sustainable Development Scenario in the period after 2040. Gas-fired power plants, though having a lower carbon intensity than coal, are also equipped with high capture rate technology, as their residual emissions would otherwise be required to be compensated by carbon removal technologies.
CO2 transport
The availability of infrastructure to transport CO₂ safely and reliably is an essential factor in enabling the deployment of CCUS. The two main options for the large-scale transport of CO₂ are via pipeline and ship, although for short distances and small volumes CO2 can also be transported by truck or rail, albeit at higher cost per tonne of CO2. Transport by pipeline has been practised for many years and is already deployed at large scale. Large-scale transportation of CO2 by ship has not yet been demonstrated (TRL 4-7) but would have similarities to the shipping of liquefied petroleum gas (LPG) and LNG. Nonetheless, considerable possibilities for innovation remain, in particular for offshore unloading of CO2, and spillovers from the general shipping industry, including automation and new propulsion technologies.
Economic factors and regulatory frameworks are the main considerations in the choice of CO2 transport mode. Pipelines are the cheapest way of transporting CO2 in large quantities onshore and, depending on the distance and volumes, offshore. There is already an extensive onshore CO2 pipeline network in North America, with a combined length of more than 8 000 km – mostly in the United States. These onshore pipelines currently transport more than 70 Mt/year of CO2, mainly for EOR. Combined with new policy incentives, including the 45Q tax credit, the vast existing pipeline network in the United States has been a key driver for recent project announcements. In June 2020, the Alberta Carbon Trunk Line (ACTL) in Canada came online with a pipeline capacity of 14.6 Mt CO2, with significant excess capacity (some 90%) to accommodate CO2 from future CCUS facilities. The ACTL received CAD 560 million (USD 430 million) in capital funding from the Canadian and Albertan governments, slightly below half of the CAD 1.2 billion (USD 920 million) estimated project cost (Government of Alberta, 2020; NRCAN, 2020a). There are also two CO2 pipeline systems in Europe and two in the Middle East.
CO2 pipeline systems worldwide
Country |
System |
Length (km) |
Capacity (Mt/year) |
---|---|---|---|
United States |
Permian Basin (West Texas, New Mexico, Colorado) |
4 180 |
|
|
Gulf Coast (Mississippi, Louisiana, East Texas) |
1 190 |
|
|
Rocky Mountains (Colorado, Wyoming, Montana) |
1 175 |
|
|
Midcontinent (Oklahoma, Kansas) |
770 |
|
|
Other (North Dakota, Michigan) |
345 |
|
Canada |
Alberta Carbon Trunk Line |
240 |
14.6 |
|
Quest |
84 |
1.2 |
|
Saskatchewan |
66 |
1.2 |
|
Weyburn |
330 |
2 |
Norway |
Hammerfest |
153 |
0.7 |
Netherlands |
Rotterdam |
85 |
0.4 |
United Arab Emirates |
Abu Dhabi |
45 |
|
Saudi Arabia |
Uthmaniyah |
85 |
|
Source: IEA analysis based on IEAGHG (2013), CO2 pipeline infrastructure report 2013/18 and Peletiri, Rahmanian and Mujtaba (2018), CO2 Pipeline Design: A Review.
Existing CO2 pipeline infrastructure and CCUS projects in the United States
Open
The share of pipeline transportation in the total cost of a CCUS project varies according to the quantity transported as well as the diameter, length and materials used in building the pipeline. Other factors include labour cost and the planned lifetime of the system. Location and geography are significant factors that affect the total cost as well. In most cases, transport represents well under one-quarter of the total cost of CCUS projects. Pipelines located in remote and sparsely populated regions cost about 50-80% less than in highly populated areas (Onyebuchi et al., 2018). Offshore pipelines can be 40-70% more expensive than the onshore pipelines. There are strong economies of scale based on pipeline capacity, with unit costs decreasing significantly with rising CO2 capacity. Pipeline costs are also likely to differ substantially among regions as new projects are developed. The cost of new pipelines is estimated to be generally 30% lower in Asia than in Europe (World Bank, 2015).
While the properties of CO2 lead to different design specifications compared with natural gas, CO2 transport by pipeline bears many similarities to high-pressure transport of natural gas. Repurposing existing natural gas or oil pipelines, where feasible, would normally be much cheaper than building a new line. Design pressure and remaining service life are the two main considerations to be taken into account to evaluate the repurposing of existing oil and gas pipelines. Oil and gas pipelines typically operate at lower pressure, which leads to a reduction in CO2 transport capacity compared with higher-pressure purpose-built CO2 pipelines. Furthermore, many existing oil and gas pipelines have been in operation for more than 20 years. A case-by-case analysis is necessary to evaluate their remaining life, taking into account in particular internal corrosion and the remaining fatigue life (JRC, 2011).
Repurposing existing oil and gas pipelines for the transport of CO₂
There is considerable potential to reuse or repurpose existing oil and gas pipelines for the transport of captured CO₂ in many parts of the world. This could significantly reduce the costs of developing CO₂ infrastructure, as the investment needed to convert an existing pipeline is estimated at 1-10% of the cost of building a new one (Acorn, 2020). In addition, repurposing could help to avoid the substantial costs of decommissioning pipelines (Government of the United Kingdom, 2019). The UK Parliamentary Advisory Group on Carbon Capture and Storage and CCUS Cost Challenge Taskforce have emphasised the advantages associated with reusing oil and gas infrastructure for CO₂ transport.
Extensive pipeline networks exist in fossil fuel-producing regions. For example, there are nearly 3 million km of oil and gas pipelines in the United States (Bureau of Transportation Statistics, 2019), close to 1 million km in Canada (NRCAN, 2020b) and 45 000 km in the North Sea (IOGP, 2019). A number of technical considerations regarding the nature of the oil and gas pipeline dictate the possibilities for reuse. In particular, the pressure and moisture content of the CO₂ must be suited to the pipeline (IEAGHG, 2018a). The pipeline also needs to be reasonably close to a depleted oil and gas reservoir or suitable saline storage reservoir.
Opportunities for converting pipelines also hinge on the pace of the energy transition in each region and its impact on oil and gas demand, as well as the rate of decline in production from existing basins due to the natural depletion of reserves. For example, the UK and Norwegian sectors of the North Sea have 850 pipelines with a combined length of 7 500 km that are planned to be decommissioned over the next decade at an estimated cost of GBP 1 billion (USD 1.3 billion) (ZEP, 2020).
The Acorn CCS project in the United Kingdom (IEAGHG, 2018a) plans to repurpose an onshore pipeline (with CO2 storage in the North Sea), and the Queensland Carbon Hub/Carbon Transport and Storage Company (CTSCo) Project in Queensland's Surat Basin is also proposing to reuse existing pipelines.
CO2 transportation by ship to an offshore storage facility offers greater flexibility, particularly where there is more than one offshore storage facility available to accept CO2. The flexibility of shipping can also facilitate the initial development of a CO2 capture hubs, which could later be connected or converted into a more permanent pipeline network as CO2 volumes grow. Today, only around 1 000 tonnes of food-quality CO2 is shipped in Europe every year from large point sources to coastal distribution terminals. In recent years, interest in CO2 shipping has increased in several regions and countries where offshore storage has been proposed, including in Europe, Japan and Korea.
Large-scale transportation of CO2 by ship has not yet been demonstrated but would have similarities to shipping of LPG and LNG.4 The supply chain would consist of several steps: CO2 would first have to be liquefied and stored in tanks before being loaded onto ships for transport. Destinations may be other ports or offshore storage sites. Unloading onshore would be relatively straightforward, based on experience with current CO2 shipping operations and from large-scale shipping of other gases, such as LPG and LNG. Offshore unloading, either to an offshore platform before conditioning and injection, or direct injection to the storage site after conditioning on ship, is not yet proven and the processes are less well-understood (IEAGHG, 2020b).
Shipping CO2 by sea may be viable for regional CCUS clusters. In some instances, shipping can compete with pipelines on cost, especially for long-distance transport, which might be needed for countries with limited domestic storage resources. The share of capital in total costs is higher for pipelines than for ships, so shipping can be the cheapest option for long-distance transport of small volumes of CO2 (up to around 2 Mt/year). This would be the case with several early industrial CCUS clusters across Europe (IEAGHG, 2020b).
CO2 utilisation or "carbon recycling"
CO2 can be used as an input to a range of products and services. The potential applications for CO2 use include direct use, where the CO2 is not chemically altered (non‑conversion), and the transformation of CO2 to a useful product (conversion). Today, around 230 Mt of CO2 are used globally each year.5 The largest consumer is the fertiliser industry, which uses 125 Mt/year of CO2 as a raw material in urea manufacturing, followed by the oil and gas industry, which consumes around 70 to 80 Mt per year for EOR. Other commercial uses of CO2 include food and beverage production, cooling, water treatment, and greenhouses, where it is used to stimulate plant growth.
New CO2 use pathways, involving chemical and biological technologies, offer opportunities for future CO2 use. Many of these pathways are still in an early stage of development, but early opportunities are already being realised. There are three main categories of CO2-based products:
- Fuels: The carbon in CO2 can be used to convert hydrogen into a synthetic hydrocarbon fuel that is as easy to handle and use as a gaseous or liquid fossil fuel (see Chapter 2). The production of such fuels is highly energy-intensive and is most economically viable where both low-cost renewable energy and CO2 are available. The largest plant currently in operation is the George Olah facility in Iceland, which converts around 5 600 tCO2 per year into methanol using hydrogen produced from renewable electricity (CRI, 2019).
- Chemicals: The carbon in CO2 can be used as an alternative to fossil fuels in the production of chemicals that require carbon to provide their structure and properties. These include polymers and primary chemicals such as ethylene and methanol, which are building blocks to produce an array of end-use chemicals. The need for hydrogen and energy varies significantly according to the chemical and production pathway. An example of a company active in the field is Covestro, which is operating a facility to produce around 5 000 t of polymers per year in Dormagen, Germany. CO2 substitutes up to 20% of the fossil feedstock normally used in the process.
- Building materials: CO2 can be used in the production of building materials to replace water in concrete, called CO2 curing, or as a raw material in its constituents (cement and construction aggregates). The CO2 is reacted with minerals or waste streams, such as iron slag, to form carbonates, the form of carbon that makes up concrete. This conversion pathway is typically less energy-intensive than for fuels and chemicals and involves permanent storage of CO2 in the materials. Some CO2-based building materials can have superior performance compared with their conventional counterparts. A few applications, such as the use of CO2 in concrete mixing, are already commercially available in some markets today (IEA, 2019). Two North American companies, CarbonCure and Solidia, are leading the commercialisation of CO2-curing technology, with CarbonCure now operating some 175 facilities in the United States and Canada (CarbonCure, 2020; Solidia, 2020). The British company Carbon8 is among the companies using CO2 to convert waste materials into aggregates as a component of building materials. It is currently operating two commercial plants and aims to have five to six plants in operation by 2021 (Carbon8, 2019).
The prospects for CO2-based products are very difficult to assess, as the technologies are generally at an early stage of development for many applications. Policy support will be crucial since they are likely to cost a lot more than conventional and alternative low-carbon products, mainly because of their high-energy intensity. The market for CO2-based products is expected to remain small in the short term, but could grow rapidly in the longer term. A high-level screening of the theoretical potential for CO2 use shows that it could reach as much as 5 GtCO2/year for chemicals and building materials, and even more for synthetic hydrocarbon fuels (IEA, 2019). But in practice, these levels are unlikely to be attainable, mostly for economic reasons. Synthetic hydrocarbon fuels are unlikely to be able to compete with direct use of low-carbon hydrogen or electricity in most applications, but could become important in sectors that continue to need hydrocarbon fuels as the energy sector approaches net-zero emissions and where other fuel alternatives are limited, such as aviation. In the Sustainable Development Scenario, synthetic kerosene meets around 40% (250 Mtoe) of aviation energy demand in 2070, requiring around 830 Mt of CO2.
Large-scale deployment of CO2-based chemicals and fuels would involve large amounts of renewable electricity for their production, in particular for the generation of low-carbon hydrogen. In the Sustainable Development Scenario, the production of synthetic aviation fuels alone in 2070 requires around 5 500 TWh, which is around 8% of all the electricity produced worldwide in 2070.
The extent to which the capture and utilisation of CO2 contributes to reducing emissions varies considerably depending on the origin of the CO2 and the way the CO2 is used. Quantifying the potential benefits in each case is less straightforward than for CO2 storage as it depends on several factors.
How can CO2 use deliver climate benefits?
Using CO2 in products does not necessarily reduce emissions. Quantifying the potential climate benefits is complex and challenging, requiring a life-cycle approach. The climate benefits associated with CO2 use primarily arise from displacing a product with one that has higher life-cycle CO2 emissions, such as fossil-based fuels, chemicals or conventional building materials.
There are five main considerations in assessing the climate benefits of CO2 use:
- The product or service the CO2-based product or service is displacing
- How long the carbon is retained in the product
- The source of CO2 (from fossil fuels, industrial processes, biomass or the air)
- How much and what form of energy is used to convert the CO2
- The scale of the opportunity for CO2 use.
Understanding the potential emissions reductions associated with the displaced product or service can be difficult as they differ depending on location and may change over time (for example, as the transport fuel mix becomes less dominated by fossil fuels). The retention time of carbon in a CO2-based product also has a large impact on the climate benefits. Permanent carbon retention provides larger climate benefits than temporary carbon retention relative to the amount of CO2 used. With the exception of building materials and EOR, most CO2 use opportunities involve only temporary retention of the carbon, with it ultimately released to the atmosphere in the form of CO2.
Not all sources of CO2 are equally attractive from a climate perspective. CO2 captured from fossil energy and industrial sources and used in fuel and cement production can deliver climate benefits as long as a higher-carbon alternative is displaced. However, this would still involve emissions from the fossil or industrial sources. From an energy system perspective, products or services derived from fossil or industrial CO2 can achieve a maximum emissions reduction of 50%. This is because CO2 can be avoided only once: either it can reduce the emissions from the fossil or industrial source when it was captured or it can reduce the emissions of the final product or service. It cannot do both. Over time as fossil fuel use declines, the CO2 used must increasingly be sourced from biomass or through DAC if the energy system is to become carbon-neutral.
CO2 storage
Storing CO2 involves the injection of captured CO2 into a deep underground geological reservoir of porous rock overlaid by an impermeable layer of rocks, which seals the reservoir and prevents the upward migration of CO2 and escape into the atmosphere. There are several types of reservoir suitable for CO2 storage, with deep saline formations and depleted oil and gas reservoirs having the largest capacity. Deep saline formations are layers of porous and permeable rocks saturated with salty water (brine), which are widespread in both onshore and offshore sedimentary basins. Depleted oil and gas reservoirs are porous rock formations that have trapped crude oil or gas for millions of years before being extracted and which can similarly trap injected CO2.
When CO2 is injected into a reservoir, it flows through it, filling the pore space. The gas is usually compressed first to increase its density, turning it into a liquid. The reservoir must be at depths greater than 800 metres to retain the CO2 in a dense liquid state. The CO2 is permanently trapped in the reservoir through several mechanisms: structural trapping by the seal, solubility trapping in pore space water, residual trapping in individual or groups of pores, and mineral trapping by reacting with the reservoir rocks to form carbonate minerals. The nature and the type of the trapping mechanisms for reliable and effective CO2 storage, which vary within and across the life of a site depending on geological conditions, are well-understood thanks to decades of experience in injecting CO2 for EOR and dedicated storage.
CO2 storage in rock formations (basalts) that have high concentrations of reactive chemicals is also possible, but is in an early stage of development (TRL 3). The injected CO2 reacts with the chemical components to form stable minerals, trapping the CO2. However, further testing and research is required to develop the technology, notably to determine water requirements, which can be considerable (IEAGHG, 2017).6 There are large basaltic formations in several regions around the world, and both onshore and offshore sites have been considered for storage. Such formations also exist in places, such as India, where there may be limited conventional storage capacity, potentially opening up new opportunities for CCUS.
The overall technical storage capacity for storing CO2 underground worldwide is uncertain, particularly for saline aquifers where more site characterisation and exploration is still needed, but potentially very large. As such, it is unlikely to be a constraint on the development of CCUS. Total global storage capacity has been estimated at between 8 000 Gt and 55 000 Gt.7
The availability of storage differs considerably across regions, with Russia, North America and Africa holding the largest capacities. Substantial capacity is also thought to exist in Australia.
Theoretical CO2 Storage Capacity By Region
Open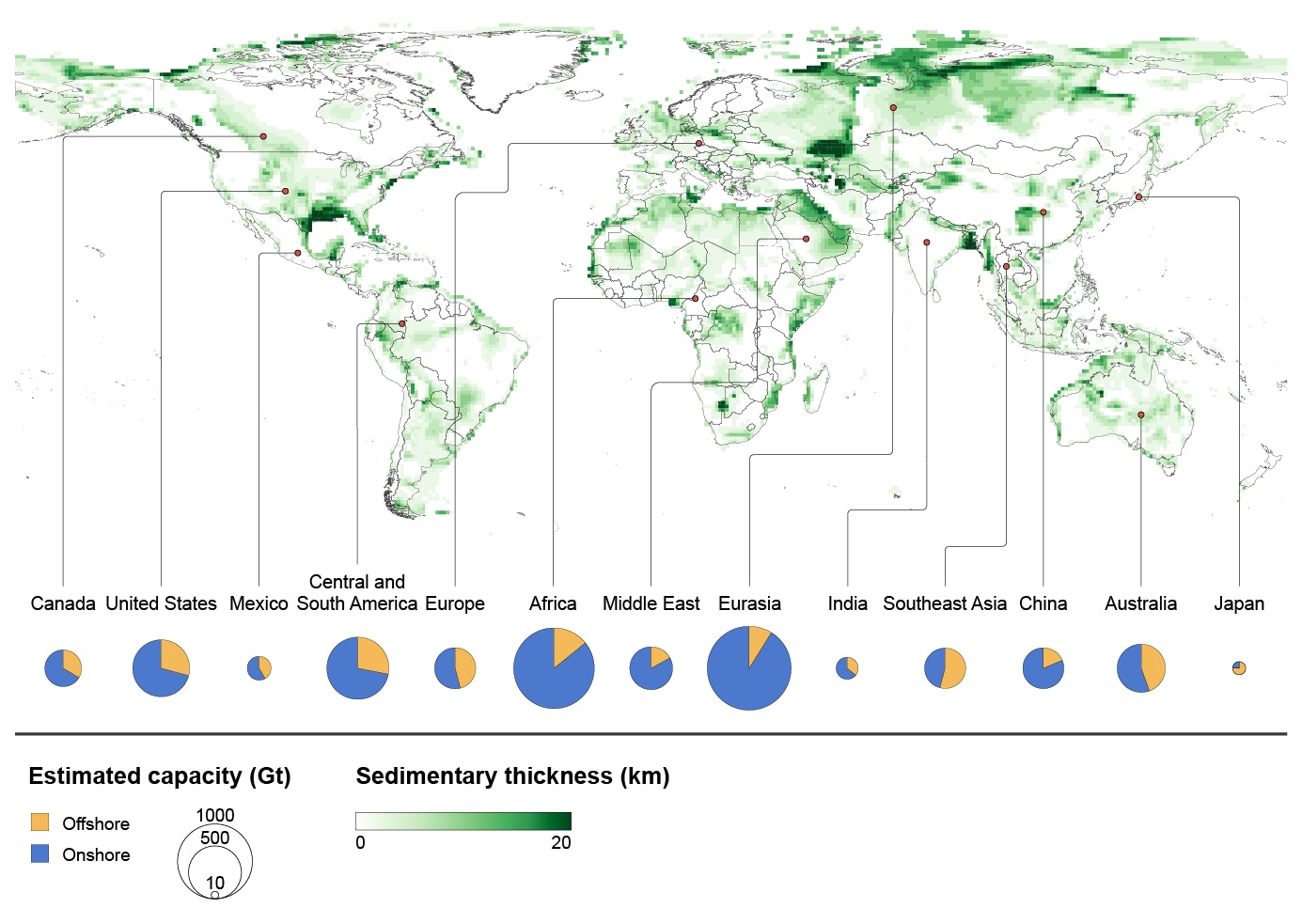
The vast majority of the estimated CO2 storage capacity is onshore in deep saline aquifers and depleted oil and gas fields. Storage capacity is estimated to range from 6 000 Gt to 42 000 Gt for onshore sites. There is also significant offshore capacity ranging from 2 000 Gt to 13 000 Gt (taking into account only sites within 300 kilometres of the shore, at water depths of less than 300 metres, and outside the Arctic and Antarctic).
Even the lowest estimates of global storage capacity of around 8 000 Gt far exceeds the 220 Gt of CO2 that is stored over the period 2020‑70 in the Sustainable Development Scenario. Despite the stark regional variation in storage capacity, only a few countries might face a shortfall in domestic storage capacity over that time frame.8
Theoretical CO2 storage capacity and cumulative CO2 storage by region in the Sustainable Development Scenario
OpenWhile notional storage volumes are considerable, a smaller fraction will most likely prove to be technically or commercially feasible. CO2 storage capacity is analogous to oil or gas insofar as it is a natural resource requiring exploration and appraisal, involving extensive data gathering. While success rates might prove to be higher than in the oil and gas exploration sector, failure rates, costs and delays in the exploration and appraisal phase are likely to be significant. The process of moving along the Society of Petroleum Engineers CO2 Storage Resource Management System (SRMS) scale from undiscovered resource status to sub‑commercial and then commercial status can take between 5 and 12 years for petroleum assets and even longer for undiscovered saline formations (OGCI, 2017). A valuable first step in characterising the progress of storage sites has been made by the OGCI’s CO2 Storage Resource Catalogue, which classifies storage sites in 13 countries following closely the definitions of the SRMS (OGCI, 2020). The majority of resource assessments are not project-based and so are automatically categorised as non‑commercial on the SRMS scale.
The possibility that CO2 stored underground could leak out has raised questions about the effectiveness of CCUS as a climate mitigation measure and public concerns about safety risks. Decades of experience with large-scale CO2 storage has demonstrated that the risk of seepage of CO2 to the atmosphere or the contamination of groundwater can be managed effectively. The probability and potential impact of such events have been studied comprehensively and have been found to be generally low, with risks declining over time. Nonetheless, careful storage site selection and thorough assessment is critical to ensure the safe and permanent storage of CO2 and to reduce risks to acceptable levels. Thorough assessment includes detailed modelling of the anticipated behaviour of the CO2 over time, together with ongoing monitoring, measurement and verification. A robust legal and regulatory framework is important to ensure appropriate site selection and safe operation of geological CO2 storage sites. This already exists in many countries. Project developers and the public authorities have to address public concerns through effective stakeholder engagement.
The cost of developing CO2 storage sites will be an important factor in how quickly CCUS is deployed in the coming decades in some regions, though generally costs are expected to be low relative to CO2 capture. Current and estimated CO2 storage costs vary significantly depending on the rate of CO2 injection and the characteristics of the storage reservoirs, as well as the location of CO2 storage sites. The cost of developing new sites, especially where CO2 storage has not been carried out before, is very uncertain, particularly with regard to the effect of reservoir properties and characteristics.
In some cases, storage costs can be quite low. Indeed, when the CO2 is stored as a consequence of CO2-EOR operations, the cost of storage can effectively be negative net of the incremental revenues from oil production. More than half of onshore storage in the United States is estimated to be below USD 10/tCO2, which would typically represent only a minor part of the overall cost of a CCUS project. Depleted oil and gas fields using existing wells are expected to be the cheapest storage option. A small number of storage reservoirs with less favourable storage conditions are caught in the asymptotic parts of the curve. About half of offshore storage is estimated to be available at costs below USD 35/tCO2. Similar cost curves are expected to apply in other regions, but further research is needed to confirm this (Rubin, Davison and Herzog, 2015).
Indicative CO2 storage cost curve for the United States, onshore
OpenIndicative CO2 storage cost curve for the United States, offshore
OpenThe potential for CO2 storage through EOR
The oil industry is the largest consumer of externally sourced CO2, with an estimated annual global consumption of around 70 Mt to 80 Mt (in 2017) for EOR (US EPA, 2018). CO2-EOR is a well-established commercial technology that has been applied since the 1970s, primarily in the United States. The technology involves the injection of CO2 into oilfields to enhance production. This increases the overall reservoir pressure and improves the mobility of the oil, resulting in a higher flow of oil towards the production wells. The United States continues to dominate the CO2-EOR industry, which is facilitated by an extensive pipeline infrastructure of around 8 000 km. Other countries applying CO2-EOR, but on a smaller scale, include Brazil, Canada, China and Turkey. The majority of purchased CO2 is currently produced from underground CO2 deposits; for example, in the United States, less than 30% of the CO2 is derived from non‑geological sources, mainly due to the absence of available anthropogenic CO2 sources close to oilfields (IEA, 2018).
Today, between 0.3 t and 0.6 t of CO2 is injected in EOR processes per barrel of oil produced in the United States, although this varies between fields and across the life of projects (IEA, 2018). During the process, a portion of the CO2 remains below the ground, while the remainder returns to the surface as the oil is extracted.9 Most CO2-EOR projects recycle CO2 returning to the surface as it is an expensive input to the production process, resulting in over 99% of the injected CO2 being permanently stored over the life of the project. The cost of CO2 is generally linked to the oil price and can range from around USD 15/t to USD 30/t of CO2. Injecting 0.5 tCO2 per barrel of oil produced would therefore cost USD 7.5/bbl to USD 15/bbl (IEA, 2018).
Globally, an estimated 190 billion bbl to 430 billion bbl of oil are technically recoverable with CO2-EOR. This would require injecting between 60 billion t and 390 billion t of CO2 (IEA, 2018), compared with total energy-related emissions of CO2 of around 33 billion t in 2019. The United States has the greatest potential, but there are also good prospects in Central Asia, the Middle East and Russia. Today, the key obstacles to wider deployment of CO2-EOR are high capital outlay for projects, suitable geology, a lack of CO2 transport infrastructure, and limited availability of low-cost and reliable sources of CO2 in close proximity to oilfields.
CO2-EOR has the potential to deliver climate benefits but assessing the net impact on emissions requires a quantitative life-cycle assessment, involving modelling of oil market dynamics and taking account of project-specific characteristics. The results of IEA modelling suggest that the net emissions savings from EOR using CO2 from anthropogenic sources can be significant, amounting to 0.5 t to 1.5 t of CO2 per tonne injected, depending on the configuration of the project and the type of oil displaced (IEA, 2015). These results are broadly in line with those of studies of life-cycle emissions using data for the United States (Azzolina et al., 2016; Cooney et al., 2015). A study of the Boundary Dam project in Saskatchewan in Canada found a reduction in emissions of up to 63% across the full life cycle, which includes CO2 capture from the coal-fired power plant and CO2-EOR in the Weyburn oil field (Manuilova et al., 2014). If a non‑fossil source of CO2 is used and the amount of CO2 stored exceeds the emissions from the production and combustion of the oil itself, the oil could be described as net “carbon-negative”. In other words, to produce “carbon-negative oil” – that is for CO2-EOR actually to reduce the stock of CO2 in the atmosphere – the CO2 either has to come from the combustion or conversion of biomass or has to be captured from the air.
Cost reduction potential
There is considerable potential for reducing costs along the CCUS supply chain. Some of the factors that will drive cost savings are specific to the different stages along the chain – capture, transport, use and storage – while others apply to all stages. Across the supply chain, cost reductions could be achieved in a number of ways:
- Learning by doing: There is evidence that the growing portfolio of large-scale CCUS projects has already contributed to cost reductions through learning-by-doing. For instance, the capture costs at Petra Nova are 35% lower than Boundary Dam, which was built just few years earlier, while a detailed feasibility study for retrofitting the Shand coal-fired power station in Canada with CCUS suggests that cost reductions of around 70% for capex and opex are possible, relative to the Boundary Dam project (GCCSI, 2019; IEAGHG, 2018b). Similarly, the Quest CCS project has identified that its capex would be 20% to 25% lower if the plant were to be built again today (IEAGHG, 2017).
- Technology spillovers: Cost reductions may come from spillover effects (see section below) and learning-by-researching. In the Sustainable Development Scenario, CO2 capture costs reduction based on learning-by-doing, learning-by-researching and spillover effects for applications in both power and industrial sectors has been estimated to be around 35% between 2019 and 2070.
- Reduced capital and operating costs: Capital costs have typically accounted for more than half of the total cost of capture at first-generation retrofitted plants. These costs can be reduced by economies of scale, improved site layout and modularisation, optimisation of the CCUS operating conditions and supply chain, and technology development. CCUS facilities can also have significant operating costs due to the additional energy required to operate the facilities, as well as solvents, chemical reagents, catalysts, the disposal of waste products and additional staff needed to run them. Operating costs can be reduced by means of optimised maintenance strategies, thermal energy and water use optimisation, increased compression efficiency, and digitalisation.
- Digitalisation: There are number of new technologies, including robotics, drones and autonomous systems, novel sensors, digital innovations, virtual and augmented reality, additive manufacturing, and advanced materials that could reduce costs along the CCUS chain. The greatest potential for reducing costs lies in the application of artificial intelligence and the internet of things in predictive maintenance and automation (IEAGHG, 2020a). The biggest scope for cutting costs using these technologies is thought to lie in storage.
- Improved business models: Business models that involve the separation of the capture, transport and storage components of the CCUS value chain, including through shared transport and storage infrastructure around industrial hubs, have potential to reduce unit costs through economies of scale while reducing commercial and technical risks. These risks increase the cost of capital and financing, which can have a large overall impact on project cost. decreases in the cost of capital in recent years have been vital to the global scaling-up of renewables (IEA, 2020c).10
CO2 capture
Reducing the cost of CO2 capture, including by lowering energy needs, has been the focus of a large amount of RD&D by private and public research centres around the world in recent years. The main potential areas for cutting both capital and operating costs include the use of innovative solvents, standardisation of capture units, modularisation and off-site manufacture, reduced contingencies, and better integration with the process plant, as well as increasing the size of facilities in order to exploit economies of scale and learning-by-doing benefits. Cost estimates for technologies at low TRLs are highly uncertain but generally, these technologies have greater potential for cost reduction than mature technologies that are well established in markets. Earlier-stage capture technologies, which could be deployed 10 to 20 years from now, could be 30% to 50% cheaper than current designs (NPC, 2019). Capture costs could also be lowered by designing innovative production technologies, such as the HIsarna steel-making process in which iron ore is processed almost directly into liquid iron using less energy and emitting less CO2 (Bellona, 2018).
Knowledge and application spillovers – the positive externalities of learning-by-doing or learning-by-researching that increase the rate of innovation in a technology area that was not the target of the original innovation effort – can also bring down the cost of CO2 capture. For instance, in the Sustainable Development Scenario, the learning gained from various applications of chemical absorption in industry and power generation (e.g. when CO2 needs to be separated during standard process operations without being stored or used) cuts the cost of deploying this technology for CCUS by around 12%.
Cumulative capacity and capture cost learning curve for CO2 chemical absorption in coal-fired power generation and small industrial furnaces in the Sustainable Development Scenario, 2019-2070
OpenIn power generation, capture costs are expected to be reduced by the adoption of various emerging technologies. For instance, electrochemical separation is projected to lower the LCOE with CO2 capture by 30%; chemical absorption with advanced solvents and configurations, membrane separation, PSA and TSA, calcium looping, and cooling and liquefaction by between 10% and 30%; and pressurised oxy-fuel combustion, chemical looping combustion and sorption-enhanced water gas shift by up to 10% (IEAGHG, 2019a). These cost reductions are based on the current development trajectory of these technologies, which have recently moved from the prototype to the demonstration phase. For CCUS applied to industrial process emissions, capture cost reductions can be achieved not only through innovative technologies, but also through strategies such as capturing from units emitting larger volumes of CO2 (e.g. recovery boilers rather than lime kilns for pulp and paper production) and recovering excess heat (e.g. in steel production) (IEAGHG, 2019c).
Transport and storage
CO2 transport by pipeline is a mature technology, with practical experience spanning several decades, mostly in North America. The maturity and relative simplicity of the technology has resulted in few technological improvements that have affected costs since the 1980s. Experience with CO2 storage over the last decade has also grown, including with five dedicated storage operations (i.e. not associated with EOR) but the site-specific nature of geological storage makes it difficult to discern clear downward cost trends.
The main scope for reducing costs is by exploiting economies of scale through pooling of transport and storage demand. This can be achieved by developing industrial clusters with shared infrastructure (see Chapter 1). In some cases, the repurposing of existing oil and gas pipeline infrastructure could contribute to lowering costs (see above).
CO2 transport and storage are expected to benefit from technology innovation and digitalisation that are currently revolutionising the oil and gas industry. The largest cost reductions are likely to come from advanced sensing and real-time monitoring technologies that allow for reduced downtime and early detection of CO2 migration or leakage, due to improved tracking and predictive maintenance11 (IEA, 2017). Drones, robotics and automated systems will be particularly important as they can significantly reduce the need for labour, for example on offshore storage platforms. Smart drilling and developments in seismic analysis could also accelerate site appraisals and reduce costs. The potential for cost reductions through innovation is greater for CO2 storage for which the costs of new projects are projected to fall by around 20-25% by 2040, (IEAGHG, 2020a).
References
Membranes can also be highly selective to another permeate (such as hydrogen) and let that one through, retaining CO2.
The CO2 concentration of raw natural gas varies considerably by reservoir, ranging from CO2-free natural gas in Siberian fields to exceptionally high shares of 90% CO2 content in some fields in South-East Asia. Raw natural gas produced from the Norwegian Sleipner field has a CO2 concentration of 9%, which is considered to be high compared to many other fields. The low capture cost is also due to the high pressure of the captured CO2 stream, which reduces cost for CO2 compression.
The remaining 25% represents the cost of transport and storage.
Several studies have investigated the potential to repurpose existing LPG and ethylene carriers for CO2 transport, but this would face significant challenges for ships that were not originally designed for CO2 transport.
This number includes both internally and externally sourced CO2. Internally sourced CO2 refers to processes where CO2 is produced and captured in a chemical manufacturing process, and ultimately consumed in a later process step; the most important example is integrated ammonia-urea plants. Externally sourced CO2 refers to CO2 that is external to the process and needs to be captured.
The CO2 is dissolved in water to speed up in situ carbonisation. This process, demonstrated at CarbFix, requires large volumes of water.
These global estimates are based on an estimated average CO2 storage capacity per cubic kilometre of sedimentary rock (Kearns et al., 2017). While this methodology has limitations, it offers a consistent approach to obtaining global CO2 storage capacity estimates.
A recent study on storage potential in Japan can be found at
www.rite.or.jp/Japanese/project/tityu/fuzon.html#up.The ISO 27916 standards provide a method for accounting the share of CO2 that is permanently stored and isolated from the atmosphere. More generally, life-cycle analysis is an important tool in determining how much CO2 is permanently removed from the atmosphere for various utilisation and storage pathways.
For example, applying a standard average real weighted average cost of capital (WACC) of 8% to a US solar PV project in 2019 yields a levelised cost of electricity (LCOE) of around USD 80/MWh. The LCOE for the same project with access to a WACC of just 4% is just over USD 50/MWh.
Predictive maintenance technologies help determine the condition of equipment in use in order to estimate when maintenance should be performed.
Reference 1
Membranes can also be highly selective to another permeate (such as hydrogen) and let that one through, retaining CO2.
Reference 2
The CO2 concentration of raw natural gas varies considerably by reservoir, ranging from CO2-free natural gas in Siberian fields to exceptionally high shares of 90% CO2 content in some fields in South-East Asia. Raw natural gas produced from the Norwegian Sleipner field has a CO2 concentration of 9%, which is considered to be high compared to many other fields. The low capture cost is also due to the high pressure of the captured CO2 stream, which reduces cost for CO2 compression.
Reference 3
The remaining 25% represents the cost of transport and storage.
Reference 4
Several studies have investigated the potential to repurpose existing LPG and ethylene carriers for CO2 transport, but this would face significant challenges for ships that were not originally designed for CO2 transport.
Reference 5
This number includes both internally and externally sourced CO2. Internally sourced CO2 refers to processes where CO2 is produced and captured in a chemical manufacturing process, and ultimately consumed in a later process step; the most important example is integrated ammonia-urea plants. Externally sourced CO2 refers to CO2 that is external to the process and needs to be captured.
Reference 6
The CO2 is dissolved in water to speed up in situ carbonisation. This process, demonstrated at CarbFix, requires large volumes of water.
Reference 7
These global estimates are based on an estimated average CO2 storage capacity per cubic kilometre of sedimentary rock (Kearns et al., 2017). While this methodology has limitations, it offers a consistent approach to obtaining global CO2 storage capacity estimates.
Reference 8
A recent study on storage potential in Japan can be found at
www.rite.or.jp/Japanese/project/tityu/fuzon.html#up.
Reference 9
The ISO 27916 standards provide a method for accounting the share of CO2 that is permanently stored and isolated from the atmosphere. More generally, life-cycle analysis is an important tool in determining how much CO2 is permanently removed from the atmosphere for various utilisation and storage pathways.
Reference 10
For example, applying a standard average real weighted average cost of capital (WACC) of 8% to a US solar PV project in 2019 yields a levelised cost of electricity (LCOE) of around USD 80/MWh. The LCOE for the same project with access to a WACC of just 4% is just over USD 50/MWh.
Reference 11
Predictive maintenance technologies help determine the condition of equipment in use in order to estimate when maintenance should be performed.